Engineers use CAD software and prototyping to explore possible dimensions for custom components. Some engineers and fabricators use geometric dimensioning and tolerancing (GD&T) to show dimensions in 3-D, including how close an object is to being a true cylinder.
GD&T cylindricity is difficult to measure. It requires advanced technology and a lot of time. Keep reading for more information about cylindricity and its applications.
Square One: Defining Cylindricity
Tolerances share how much a part’s dimensions can vary from its set measurements and still function properly. The American Society of Mechanical Engineers divides its GD&T standards into five categories: form, profile, orientation, location and runout controls.
As a form control, cylindricity focuses on the component’s shape. Cylindricity combines straightness and flatness, taking a 3-D measurement along the length of a part.
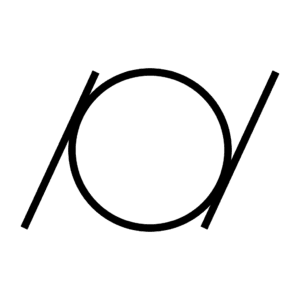
Tolerance Zones: How Far from the “Perfect” Cylinder?
You can think of cylindricity as a boundary. The part must lie within this boundary, or tolerance zone, to ensure that it is appropriately round and straight.
When applying this boundary to a drawing or blueprint, there are two zones: an outer cylinder and an inner cylinder. These two zones describe where the component’s dimensions can fall.
The component must fall within the tolerance zone. A part needs to be both round enough and straight enough. If a part does not fit within the tolerance zone, it is a failed part. It will not work for its intended purpose.
Think about a cylindrical object that must fit into a hole within another part. If the component’s straightness varies too much, the part will not pass through the hole—even if it’s perfectly round.
Common Uses for Cylindricity: Where You See It
Manufacturing blueprints utilizing GD&T may apply cylindricity to shafts and pins. Cylindricity is more common on automotive drawings and may be used when precise circularity, straightness and tapering are required.
Cylindricity measurements may be used for components like:
- Bearings
- Cylinder liners
- Hydraulic cylinders
- Pins
- Pipes
- Pneumatic cylinders
- Print rollers
- Shafts
Challenges of Measuring Cylindricity: Technology & Time
Measuring cylindricity is difficult and time-consuming. The biggest challenge of using cylindricity is the technology required to measure it. You need a roundness instrument or access to a coordinate measuring machine (CMM).
A CMM measures multiple geometric points simultaneously and more accurately than other instruments. Using a CMM can show you flatness, roundness, cylindricity and a number of other dimensional tolerances.
Not many companies are capable of using this precise type of metrology, nor can they afford the cost of purchasing and maintaining the equipment. CMMs can be affected by vibrations and heat, making them difficult to set up on the production floor.
How to Measure Cylindricity With a Roundness Instrument
- Place part on a turntable.
- Touch the instrument’s probe to the component.
- Rotate the component on the turntable.
- Manually or automatically use the instrument to identify values.
- Using a computer, plot the data on a polar graph or let a computer algorithm do the work.
- Repeat along the entire length of the cylinder.
How to Measure Cylindricity With a CMM
- Choose a cross-section and at least four points to measure.
- Manually or automatically use the CMM to record data at the points selected.
- Plot the data on a polar graph manually or have a computer algorithm do the work.
- Repeat these steps along the length of the cylinder.
What Is the Difference Between Circularity and Cylindricity?
Is cylindricity similar to circularity? The difference between these two measurements is that circularity only measures the 2-D surface of one cross-section at a time. It only measures around the surface of the circle. Cylindricity measures circularity in 3-D.
Cylindricity’s tolerance zones take circularity and straightness to cover all cross-sections at once. Both the surface of the circle and the axial part of the cylinder are included.
Cylindricity Isn’t Concentricity Either
If you’re using the 2009 version of ASME Y14.5, you’re familiar with concentricity—a dimensioning standard that’s been removed from the newest 2018 edition.
Concentricity compares the roundness of two points. These points are usually the outside diameter (OD) and inside diameter (ID) of a component.
Cylindricity is not concentricity. Cylindricity looks at the entire surface profile, describing the axis’s straightness and the surface’s circularity.
Custom Metal Fabrication & Design
Cylindricity can be helpful when exact measurements are needed. You don’t have to have a working knowledge of GD&T to design a cylindrical component. All you need to do is talk to our team!
Our engineers and fabricators will design and prototype your metal part—without bringing GD&T into the discussion. Our design and testing process ensures that the final product meets your requirements for form, fit and function.
From there, we can fabricate your parts and assemble them for your company or customer. Our degreed engineers are here to support your project, even if your team only needs assistance developing a design or blueprint for manufacturing.
Request a quote from Metaltech today. Let’s get started on your custom metal fabrication project. Cylindrical designs are welcome.