According to the US Bureau of Labor Statistics, the category of welder, cutter, solderer, and brazer jobs is expected to expand by 8 percent over the next 10 years. But, is a welding job right for you?
Welding is a stable and rewarding career choice for many people and can become a very lucrative profession when you learn to weld and as your skills advance. If you are interested in pursuing a welding career, read on to learn more about the three most common types of welding processes that you will likely learn and hone in your first few years of training.
3 Common Types of Welding Processes
by Rob Briscoe
A welding career is a good choice for many people and can become a very lucrative profession over time and with experience. The welding process is an important and essential part of the manufacturing and maintenance industries – and will likely remain so for the foreseeable future. Cars, planes, trains, and toys are made using a variety of welding techniques. This article will discuss the welding process and three of the most common types of electric welding. You will also learn about some of the benefits of each type.
Despite there being different types of welding processes and styles, all welding involves heating the materials that need to be joined together above their melting point, then joining them with or without filler metal.
The most common types of electric metal welding that we will be exploring in this article are:
- GMAW (mig);
- GTAW (tig);
- SMAW (stick) welding.
Mig Welding – GMAW (Beginning-Level Technique)
The first type of electric welding we’ll discuss is GMAW welding, which is usually called “mig” welding. This type of welding uses electricity to melt the base metals and filler wire. The filler wire is added to the base metal and is consumed during the mig welding process. This is usually the easiest welding technique to learn and is also the most common type of welding used across a variety of industries and by home hobbyists. The GMAW process can be used for carbon steel, stainless steel, tool steels, and many aluminum alloys.
Mig Welding with Solid Wire vs. Flux-Core Wire
Mig welding can be performed using a solid wire with shielding gas or with a flux-core wire. Flux-core wire is especially useful when welding in windy conditions where the shield gas would be blown away. The primary drawback to flux-cored wire is the need to remove the slag between passes. Solid wire with a shielding gas is more common in industry settings.
Mig Welding Basics
There is much more to the mig welding process than will be fully explained in this article. However, the GMAW welding process is relatively easy to learn and is normally one of the first types of welding mastered by a new welder.

To weld with a mig welder, he following steps and guidelines are typically followed(:)
- A ground is connected to the workpiece and the mig gun is brought into position, normally about ¼” off the workpiece.
- The operator feeds the wire and starts the arc by pulling the trigger on the mig gun.
- The welding current is carried along the wire until it reaches the grounded workpiece.
- The resulting spark stabilizes into a steady arc which melts the base metal and the filler wire.
- The weld wire is consumed during the GMAW welding process.
- And as a manual process, the operator is responsible for positioning the mig gun and adding the correct amount of filler wire.
The GMAW process is also used extensively by robotic welders. In this automated process, the weld parameters and start / stop points are programmed by the operator or welding technician. Once the robot is programmed correctly, it can make the welds, the same way, every time. This repeatability function is the greatest advantage for robotic welding.
Tig Welding – GTAW (Intermediate-Level Technique)
The GTAW process is commonly known as “tig” welding. This process is different from GMAW welding because the electrode – the torch in the case of tig welding – is not consumed during the welding process. The arc used to melt the metal is produced when the torch (electrode) is brought close to the grounded workpiece. The electrode is made of tungsten, and, again, is not consumed during the welding process. Instead, filler wire is added by the operator, usually by hand.
GTAW welding is more precise, cleaner, and more controllable than nearly all other welding techniques. For this reason, tig welding is commonly referred to as “white glove” welding. GTAW is less forgiving of oils, scale, and other contaminants in the weld area-both the parts to be welded and the filler metals must be clean. The parts should also fit close, with any gaps kept as small as possible.
Tig Welding Basics
The GTAW process requires the operator to control more parameters than the GMAW process, and is considered to be more difficult. Robotic GTAW (tig) welders are available, but are not as common as the GMAW robot welders. Like anything else, practice is required to master GTAW welding.
To tig weld, the operator will(:)
- Bring the electrode close to the grounded workpiece.
- Use a foot or thumb controller to control the arc intensity by adjusting the amperage (in most common tig welding processes).
- Start the arc – once the tungsten electrode is close enough to the workpiece – with the controller slid up (thumb control) or by pressing the toe side of the foot controller.
- Back off the amperage once the arc is stable. The parts will be heated by this arc.
- Once the base metals each have a good puddle of molten metal, dip the filler wire into the puddle.
- This will melt the filler wire into the base metal and fill the area between the base metals.
- Move the arc to melt the base metal, and dip the filler wire into the puddle again.
- This ‘dip-dip-dip‘ of the filler wire gives the GTAW welding process the common “stacked dimes” look.
Stick Welding – SMAW (Intermediate-Level Technique)
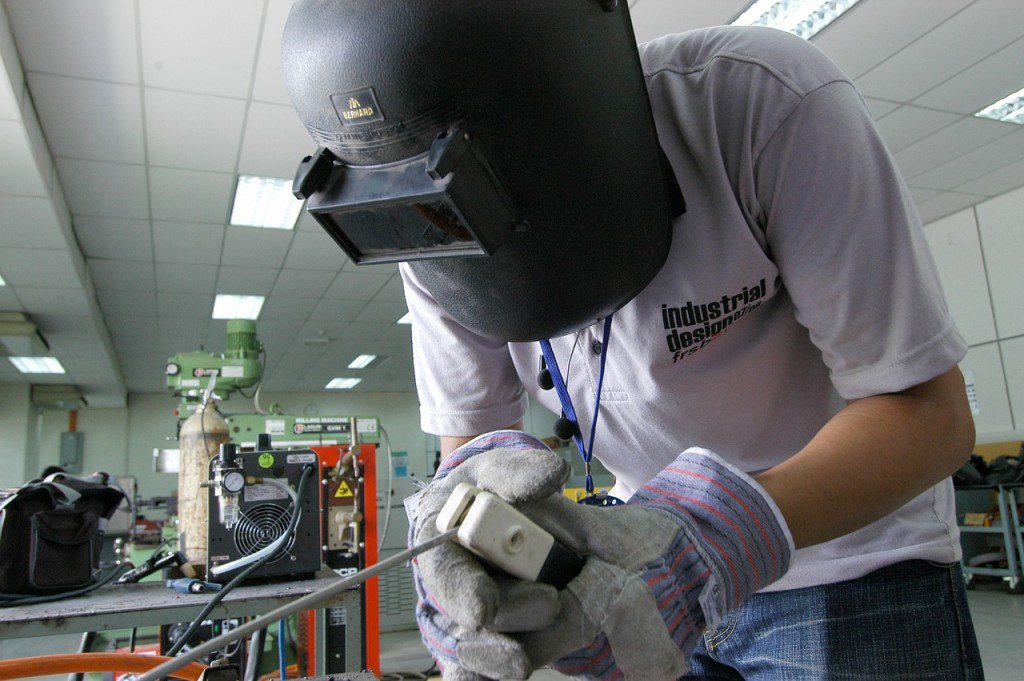
The SMAW process is more commonly known as “stick” welding. Like the GMAW process, the electric current is carried by the consumable electrode in the form of a welding rod. Unlike the tungsten electrode in the GTAW technique, the welding rod in SMAW is consumed during the welding process. This process is ideal for use outdoors or in conditions that would blow shielding gas away if GMAW or GTAW processes were used.
The equipment used in stick welding is simple to purchase and operate and is usually inexpensive. A solid flux is also melted during the weld process. The purpose of the flux in the SMAW technique is to protect the molten metal while it cools. If the volt and amp settings are correct, the flux coating (slag) is normally easy to remove, and will often fall off by itself.
Stick Welding Basics
- To start the arc with stick welding, a welding rod is placed in the electrode workholder.
- The workpiece is grounded.
- The welding rod is touched lightly to the workpiece in a manner similar to striking a match.
- The resulting arc is stabilized when the operator achieves the correct distance between the welding rod and the workpiece.
Stick Welding Safety Note
Some welders will guide the welding rod with their gloved hand instead of using the electrode holder. This practice is not safe and is not recommended. Doing this may allow the welding current to pass through your body instead of the welding rod.
Overall, SMAW, or stick welding(,) is considered to be more difficult than GMAW (mig) welding. However, the advantage of being able to weld outdoors and low cost of equipment and supplies makes this a popular type of welding to learn and hone. With practice, this type of welding can be mastered and used successfully on the farm or factory.
The Final Word: Is a Welding Career for You?
We have only discussed three of the main types of welding processes – Mig (GMAW), Tig (GTAW), and Stick (SMAW) – in this article. There are approximately 100 types of welding processes used in the industry today. The three types presented here, however, do cover about 90% of arc welding techniques used in production, fabrication, and repair industries.
A person interested in becoming a welder, either for hobby or as a career, should consider one or more of the primary welding processes like the ones explored in this article. Further, it is always a good idea to pursue welding certification courses and tests to pass AWS D1.1 standards. This is a very good way to prove the quality of your welds, both to yourself and to a future or current employer.
So, is a welding career for you? If the processes and prospects discussed in this article interest you, chances are, the answer is “yes.” Additionally, if you already have a hobby involving cars, you have likely found yourself needing to weld something. Overall, as long as there are parts made of metal in any industry, a welder will be required. So, why not pursue a welding job to make money doing something interesting and rewarding?