Cutting is essential to the metal fabrication process. It’s the first step in any project that’s ready to start production. Depending on what you need to accomplish, cutting components could be achieved by a punch press or automated saw. However, laser cutting machines can do the job efficiently and accurately when you need a precise cut every time.
Is laser cutting right for your fabrication project? Let’s dive into what you should know about laser cutting metal and other materials.
How Does Laser Cutting Work
What is laser cutting, and how does it work? Laser cutting is a contactless process that can be used with both metal and non-metal materials. When a laser beam hits a workpiece, that area of the workpiece is heated until it melts and vaporizes.
During this process, the laser beam focuses on one small site at a time—not the entire workpiece. If one area is heated long enough, the laser’s heat will penetrate through the workpiece completely. Note the tool itself never touches the workpiece.
CO2 Laser Cutting Machines
CO2 laser cutting machines use electricity and an assist gas to operate. Many CO2 lasers require either a pre-charged, sealed or delivered assist gas, such as oxygen or nitrogen, to refine the beam’s cut based on the material and specifications.
If you are working with thick materials, CO2 lasers deliver faster straight-line cutting and a smoother surface finish. They efficiently cut through materials greater than 5 mm and have a quicker initial piercing time when compared to fiber lasers.
Fiber Laser Cutting Machines
Fiber lasers use diodes to create the laser’s light. Optical fibers doped in rare earth ions, such as Erbium, Ytterbium or Thulium, amplify light to cut materials. Fiber laser cutting machines work at faster speeds and use less power than CO2 laser cutting machines.
If you need to cut thin or reflective materials, a fiber laser cutting machine is best for the task. They slice thin materials quickly, and the machine won’t be affected by back reflections. Fiber lasers have a much smaller cutting focal point, making them ideal for marking serial numbers or barcodes, too.
What Are the Advantages of Using a Laser Cutter?
The possibilities are almost endless with laser cutting. Depending on your application, laser cutting may work best to cut materials for your project. High-speed laser cutting can help reduce material waste and get that precise cut you need for your custom parts.
Here are six advantages of laser cutting:
- Accuracy. Laser cutting vaporizes materials quickly, producing very accurate cuts. Often, minimal to no post-processing needs to take place after laser cutting. The heat from the small, focused laser produces precise, smooth edges, leaving little to no melted material or distortion behind.
- Complexity. Does your blueprint require intricate details? Are your custom parts a unique shape or size? Laser cutting can handle the most complex geometries while placing minimal stress on the rest of the workpiece.
- Materials. You can cut almost any material with a laser cutting machine: steel, aluminum, brass, stainless steel, copper, and even plastics. Laser cutting is perfect for working with thin materials because the laser beam moves quickly and doesn’t heat the material to the point that it warps.
- Versatility. A laser can cut through almost any material to produce an exact shape or contour time and time again. It can also do more than flat cutting. Laser cutting machines can perform drilling, marking and engraving tasks, too.
- Repeatability. Laser cutting is perfect for component parts that need to meet exacting standards on each piece. With a laser cutting machine, you can expect the cut parts to be exact replicas of one another.
- Higher sheet utilization. Want to get the most out of every piece of sheet metal? Laser cutting techniques, like nesting cut parts, can help you get more out of your raw materials depending on the part’s design.
What Are the Disadvantages of Laser Cutting?
Though laser cutting offers extreme accuracy, it’s not the right process for every fabrication project. Laser cutting is not recommended for thicker materials. At Metaltech, the maximum material thicknesses we can laser cut are 20 mm or 1″ for steel, 15 mm or .60″ for stainless steel, and 10 mm or ½” for aluminum.
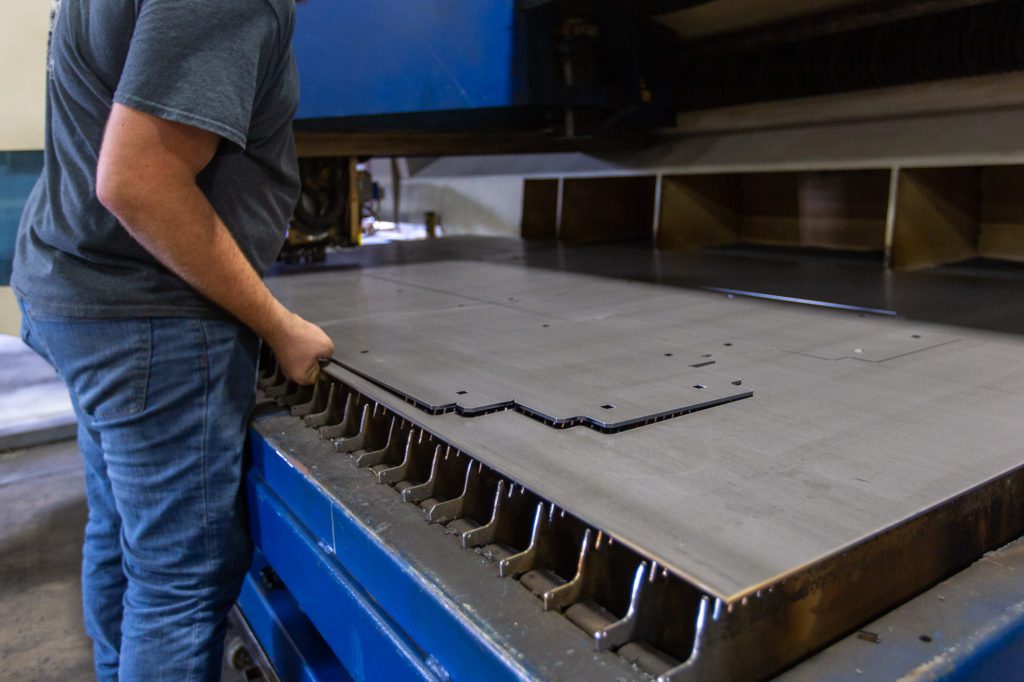
Laser Cutting Metal & More Across Industries
Many industries use laser cutting to reproduce precise replicas of parts. We have years of experience working with diverse industries to fabricate and powder coat their component parts to the required specifications. Often, laser cutting is used in the following industries:
- Automotive. Laser cutting helps create vehicle body pieces, electronic parts, carriage components, and even interior buttons.
- Medical. Medical devices, like stents, are made from laser-cut parts and materials. Other medical equipment, like tubing, can be laser-cut as well.
- Electronics. From metal casings to circuit boards, laser cutting helps electronics manufacturers cut small, precise parts.
- General manufacturing. Laser cutting can be used to produce component parts for airplanes, appliances, furniture, lighting, tools, and much more.
Ready to start your metal fabrication project?
Contact Metaltech to learn more about our laser cutting capabilities or request a quote today to start your next project.