In 1962, General Motors was the first to add a welding robot to a production line. Though robotic welding came on the scene in the mid-twentieth century, it didn’t take off until the 1980s as more and more automotive manufacturers started using the technology for vehicle bodywork.
Today, manufacturers across industries employ welding robots to produce accurate and repeatable welds. The majority of robotic welding systems across the world perform spot welding. However, many perform arc welding, including MIG (GMAW) and TIG (GTAW) welding. Globally, the robotic welding market is expected to grow by 8.7% between 2019 and 2026.
What Is Robotic Welding?
Here’s what you need to know about robotic welding, whether you only require welding services or you need a company to complete the entire fabrication process.
Robotic welding systems automate welding operations, and they may be fully- or semi-automated. Fully-automated systems load and unload parts from the workcell, whereas semi-automated systems require a human operator to guide parts and products to and from the cell. Though a robot does the welding, certified human operators are still needed to program and monitor the robot’s work.
Each system has a control interface that allows the operator to input information. Once programming information is entered, the system’s controller communicates with the robot and shares how to execute the task at hand.
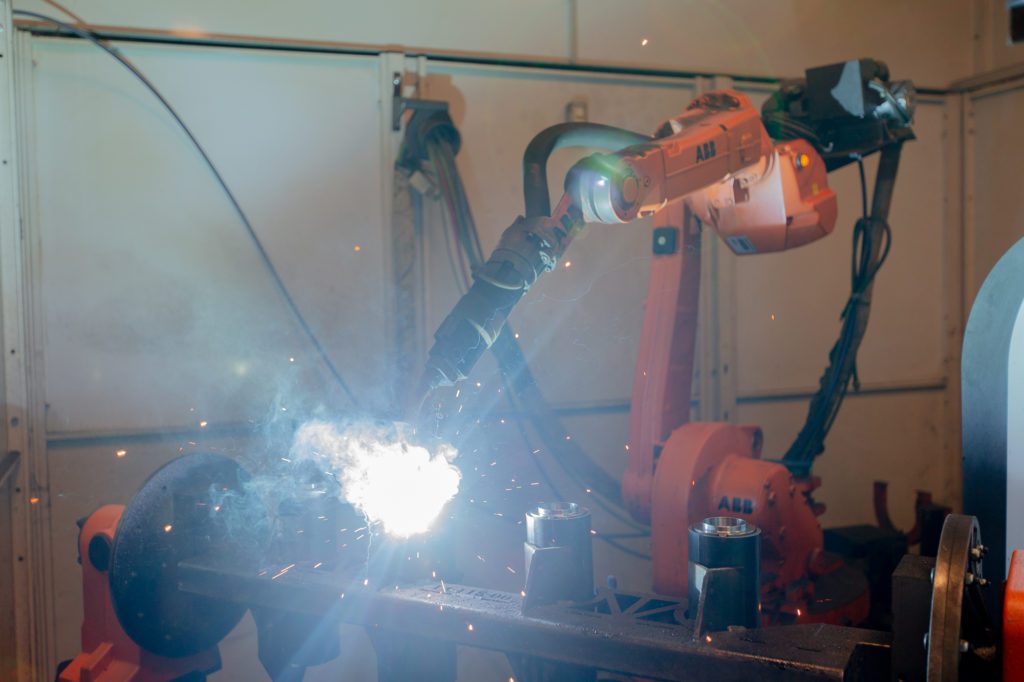
How Do Welding Robots Work?
Robotic welding systems include a power supply, fixtures, a robotic arm, a torch and a wire feeder. The robotic welding arm’s reach and the machine’s weight-carrying capacity affect the size of the parts it can weld. All weld points must be within the arm’s reach.
Welding can begin once the system is programmed and parts are in the workcell. A robot welding operation generally follows these steps:
- Parts are positioned by fixtures within the robotic welding cell. These fixtures hold the metal in place during the welding process.
- A certified operator selects the program for the robot from the control panel.
- The power supply provides heat for the welding torch, which is attached to the end of the robotic welding arm.
- A wire feeder provides the robot with filler wire as needed during the welding process. The feeder connects to the torch by a whip or torch cable.
- The robot identifies the weld point(s), moving the robotic welding arm and torch to the correct area(s).
- After completing the weld, the machine stops and the welded parts can be removed from the fixture.
- The robotic welding arm moves the torch to a cleaning station, where metal splatter is removed to maintain the integrity of future welds.
At Metaltech, our robotic welding capabilities are for MIG welding, which is also known as GMAW.
Manual Welding vs. Robot Welding: Which Is Better?
While robotic welding offers many advantages, there is a place for both humans and robots in fabrication. As mentioned above, welding robots still need human operators to program them and troubleshoot errors.
When will a fabricator recommend robotic welding? Is it best for every project? Fabrication companies use robotic welding machines on high-volume projects that require exact repeatability. Automotive, fabrication and metal industries rely on welding robots to deliver large quantities of repeat welds.
Manual welding is often used for smaller volume projects, simple parts, parts that require human judgement, or parts that are larger or more complex than the capabilities of the robot. Expert welders can work quickly on certain projects with flexibility that isn’t available with a robot.
Fabrication companies rely on both humans and robots to complete the unique welding projects that come their way. When you work with a fabrication shop, they can tell you whether manual or robotic welding is best for your project.
Robotic Welding Issues & Challenges
Investing in a robotic welding system is a hefty upfront cost for fabrication companies, though it does pay for itself over time. Those looking for welding services should keep in mind that robotic welding may not be the right choice for a project, depending on its volume and complexity. There are some things only a human welder can do!
Some of the disadvantages of welding robots include:
- Less flexibility. Robotic welding machines perform the same task over and over again. They have to be programmed to change their tune. Expert welders can easily change welding types when required for a project.
- No ability to react. Human beings respond when things go wrong and take action to course-correct. Robots will continue performing the same tasks—even if it includes a mistake—until they are stopped and reprogrammed.
- Not for small projects. It takes a robotic welding operator time to program the system. If the robot won’t be in use for a repeat job, it’s not an efficient use of time to program it. A human team can quickly complete smaller volume or one-off projects, which is why those projects are often better suited for manual welding.
Advantages of Welding Robots
When you need to complete hundreds of repeat welds, robotic welding systems can do the task more efficiently and accurately than a team of human welders. Robots allow companies to expand their offerings and capacity.
What other benefits come with using a welding robot? Below are a few advantages of robotic welding:
- Great for large projects. A robot has better endurance than a human welder, which is why they are preferred for high-volume runs. When you have a lot of parts to fabricate, robotic welders simply don’t get tired and can keep the work flowing.
- Incredibly accurate. Repeatability is the best benefit robot welding systems bring to the table. Robots perform uniform welds time after time. Though there is still a chance the technology will make a mistake, errors happen less often than with manual welding.
- More efficient. Welding robots don’t require breaks or downtime and can perform tasks 24/7. Robots also have a much higher arc-on time than human welders. For larger projects, robotic welding helps increase efficiency.
- Produces less waste. Even the most experienced human welders make mistakes during a project. When an error is made, the metal is scrapped. Robotic welding creates less waste due to its high level of accuracy.
Metaltech Products, Inc. has the welding capabilities you need to complete your project, whether you only need assistance welding or you’d like us to work with you from start to finish. We have almost 15 years of robotic welding experience, and we continue to enhance our capabilities by bringing in new technology. If manual welding is what you need, our certified welders perform MIG, TIG and resistance spot welding for component parts across a variety of industries.
Request a quote from us to discover which type of welding is right for your custom metal fabrication project.