Forget wet paint. Try a dry finish. Powder coatings are excellent choices for that final film of color, texture or protection. According to the Powder Coating Institute, powder coating is a more economical and environmentally friendly alternative to liquid paint, and it’s been around since the 1960s.
Compared to liquid paint, powder coat finishes are more durable, attractive and resistant to corrosion and chemicals. The powders used are made of polymer resins that adhere to metals when electrically charged. During the application process, an electrostatic gun sprays the powder onto a grounded metal surface.
Different powder coat types offer special properties and effects. Let’s dig into the types of powder coatings and their characteristics.
Two Types of Powder Coatings
Powder coatings are made of polymer resins, pigments and curing agents. Together, these ingredients mix to make colorful powders that adhere to metals when charged. There are thousands of powders and combinations, meaning that there are almost infinite possibilities for the color, texture and physical properties of a powder coat finish.
There are two broad categories of powder coatings: thermoplastics and thermosets.
Thermoplastics
Thermoplastics are synthetic materials that soften when heated. You can melt thermoplastics at high temperatures, which means these types of powder coatings can be reformed and recycled. Powder coatings that are reversible and reusable have their perks, but they are not suitable for environments with intense heat.
Thermoplastic powder coatings are more durable than thermoset coatings because you can apply thicker layers without the coating becoming brittle. Manufacturers apply thermoplastic coatings to metal parts, auto parts and kitchen appliances.
Thermosets
Thermoplastic coatings can become liquid, eliminating all chemical bonds. Thermosets, on the other hand, experience a chemical cross-linking reaction when heated. This reaction changes the properties of the plastic, causing it to form a solid coating.
A thermoset powder coating can’t be recycled since chemical bonds form as the powders cure. These chemical bonds prevent thermosets from melting, which makes them ideal choices for high heat environments. Some thermoset powder coatings can withstand up to 1,000 degrees Fahrenheit.
Though they have an extraordinary resistance to heat, thermosets have a disadvantage: they become brittle the thicker they are applied.
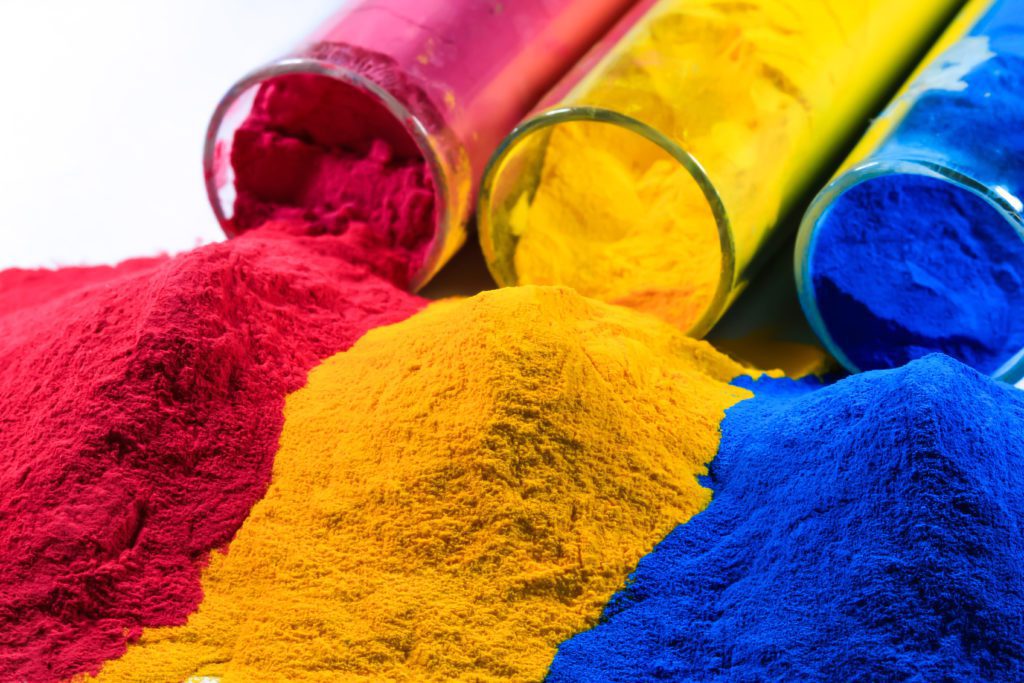
Common Powder Coat Materials
A powder’s polymer resins can be mixed with other materials or ingredients to create unique looks and textures. Depending on the materials used, a coating may become stronger, more resistant to fading or protected from corrosion.
Thermoplastic Powder Coat Materials
Polyesters
Manufacturers apply polyester powder coatings to many products, including outdoor furniture, fencing and auto parts. These coatings come in an array of colors and gloss levels. Leave polyester-coated products outside, and they will weather the elements well while resisting impacts and abrasions. Most polyester powder coatings offer one to three years of UV resistance.
Polyester coatings maintain color and gloss when exposed to UV light, only experiencing minor fading over time. While polyesters can handle the sun, they have a lower resistance to chemicals. Super durable polyester powder coatings work best for pieces that will remain outside permanently.
Nylons
Nylon powder coatings have a solid resistance to solvents and oils. They can withstand impacts and abrasions and are primarily used for protective applications. Many industrial parts manufacturers safeguard their components with nylon powder coatings because of their strength.
Polyvinyl Chlorides (PVC)
Approved by the FDA, polyvinyl chloride coatings can be used in industries that require food contact. Polyvinyl chloride coatings are pliable and durable, and they can also be used as insulators for electric lines.
Polyolefins
Polyolefin is a thermoplastic that’s resistant to abrasions and chemicals. With its great adhesion properties, a polyolefin powder coating produces a final finish with a very smooth surface. Many lab equipment parts are coated with polyolefin because the sleek surfaces are easy to clean again and again.
Polyurethanes
Polyurethane powder coatings have strong weathering characteristics and anti-corrosion properties. They have a resistance to humidity as well as resistance to many chemicals and oils. Polyurethane’s versatility means it can be used to coat interior decorations and outdoor products that remain exposed to the elements.
Fluoropolymers
Fluoropolymers offer great weathering properties and amazing color retention. Due to these characteristics, architectural markets use fluoropolymers for exterior elements like windows and doors. The most common types of fluoropolymers are FEVE and PVDF. FEVE resins have superior one coat capabilities and excellent outdoor performance. PVDF resins always need a primer beneath them.
Urethanes
Urethanes are similar to polyesters, but they use different curing agents. These types of powder coatings leave a smooth finish while maintaining good exterior durability. Fuel tanks, agricultural equipment, car rims, and even doorknobs are coated with urethanes because of their appearance and resilience. A word of caution: At greater thicknesses, urethane powder coatings can become brittle and outgas.
Thermoset Powder Coat Materials
Epoxies
Epoxies are some of the most widely used powders. They adhere to metals exceptionally well and provide excellent chemical and corrosion resistance. As a finish, epoxy powder coatings are smooth and uniform.
Epoxies are mainly used for indoor products because they don’t weather well. Despite their chemical resistance, epoxy powder coatings can only take minimal UV light exposure. Outside, the coatings fade easily under the sun and become brittle and chalky after only a few months.
For these reasons, manufacturers commonly apply epoxies as primers.
Epoxy-Polyester Hybrids
Indoor appliances, shelving, interior lighting and children’s toys are often coated with epoxy-polyester hybrids. When combining polyesters and epoxies, you get a softer coating with greater weather degradation properties than pure epoxy coatings. Adding polyester helps create a smooth, thin finish, and it adds to the coating’s weatherability. However, polyester reduces epoxy’s natural chemical resistance.
Epoxy-polyester powder coatings are less likely to chip or crack compared to pure epoxy, and they are less likely to chalk outdoors.
Acrylics
Acrylics leave high gloss finishes that give off a wet appearance. Many automotive parts, like wheels and exposed engines, are coated with acrylic materials. Acrylics differ from epoxies in that they fare well in UV light.
Silicon-based Powders
Silicon-based powders are made of silicone resins and curing catalysts. They can withstand high temperatures—up to 1,000 degrees Fahrenheit. Exhaust systems, motorcycle parts and oven racks are all finished using silicon-based powder coatings because of their impressive ability to resist heat.
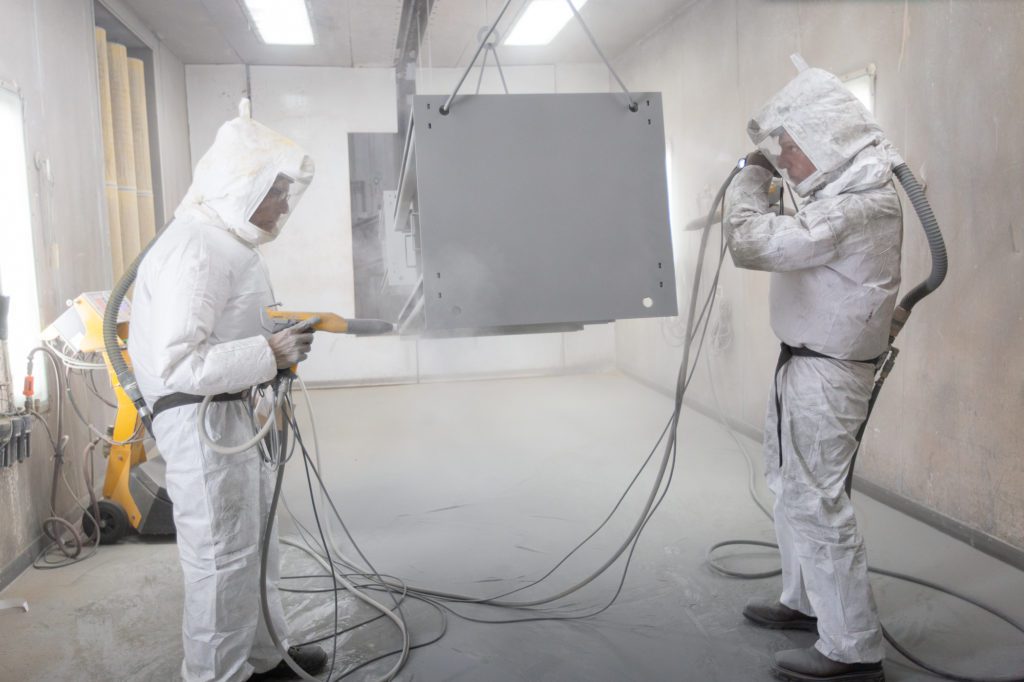
The Final Finish: Powder Coating Finish Types
Powder coatings aren’t only for longevity and part protection. They come in various colors, textures and glosses that allow you to customize the part’s appearance. Powder coatings help you achieve the look you desire—from neon colors to finishes that glow in the dark.
Gloss
The gloss level refers to the sheen of the powder coating. Matte finishes are flat, and they help hide any imperfections that are on the metal. Glossy finishes have less surface friction, so they are easier to clean. However, the higher the gloss level, the more the finish brings out imperfections in the part’s surface. High gloss finishes are often used on components in the medical and food industries since they are easier to clean.
Texture
Adding to the texture of a part’s surface can be purely cosmetic or meant to enhance a part’s usability. Many textured powder coatings help hide imperfections on the metal’s surface. Safety applications may also require texture to create non-slip or easy-grip surfaces.
- Sand: A sand-like texture increases friction and can help with safety requirements.
- Wrinkle: These coatings are one step above the sand texture. Wrinkled coatings are rougher, and they offer the end-user a better grip.
- Hammered: Similar to the bumpy surface of a golf ball, hammered textures add durability and create a glossy appearance.
Metallic
Many types of powder coat materials can be combined with metallics to create a metallic finish. Applying a metallic finish has added challenges. Metallics react differently during the electrostatic process. Much like how metal filings follow a magnet, metallics follow the electrostatic gun during the powder coating process, making it hard to apply a uniform coat to large areas.
Custom motorcycles, upgraded rims and other luxury metal items have metallic powder coatings. If a metallic powder coating is what you need, it will take more planning and research to produce the best result.
As you prepare for your next project, consider how customers will use your metal component. Will the part be exposed to high heat or constant sunlight? Does it need to be scratch-resistant or come in a unique color? Finding suitable powders for your application is something we can help you accomplish.
Request a quote from Metaltech. We offer powder coating services along with custom metal fabrication. Put the finishing touches on your component parts, or work with us from design to delivery.